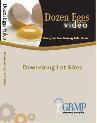
Description
Do You Really Need A Dozen Eggs to Bake A Cake?
As customers, we have come to expect perfection in quality and delivery and we don’t expect to pay extra for it. But something mysteriously occurs as we enter our workplaces: we become suppliers and our point of reference changes. We are governed by supply side rules which place our needs ahead of the customers’. Policies like AQL (acceptable quality level) and EOQ (economic order quantity) rationalize quality standards and provide incentives to provide products or services that the customer does not need. We do these things to “optimize” and to be “efficient”, erroneously thinking that such practices will reduce costs and increase profits. In the name of profit improvement we also “standardize” product and service offerings, thereby limiting customer selection.
Customer-first thinking, a keystone of the Toyota Production System, notes simply that we should provide the customer’s exact order immediately with perfect quality. Yet in our workplace we are faced with policies and measures which obscure that view.
“Dozen Eggs” illuminates customer-first thinking by taking viewers on a journey to buy ingredients for a cake – including one dozen eggs. The scenario raises questions regarding quantity and quality from a customer standpoint. How many eggs are really needed to bake a cake? How much supply side thinking is contained, for example, in units of measure like one dozen eggs? For whom is this quantity “economical”? And what is the customer’s acceptable level of quality? Is one cracked egg acceptable? What role does inventory play in providing excellent service to the customer, and what role does it play in the price the customer pays?
Using direct observation of familiar tasks and class participation techniques, “Dozen Eggs” detaches viewers from the conventional supplier-first viewpoint that thwarts many Lean initiatives. This 36-minute DVD is both for policy makers and those who must execute those policies.